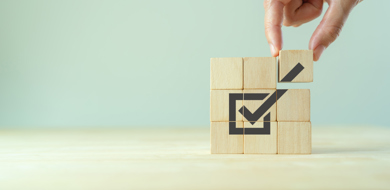
In control
Quality Assurance
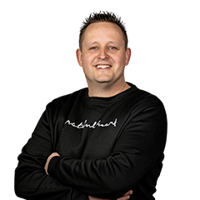
Our department
Quality Assurance (QA)
ISO 9001:2015
Annually we renew our ISO certificate. The ISO is assessed through internal and external audits. Every year we carry out two internal audits to evaluate our management system. These audits are conducted by Consultancy Kleemans, which provides us with tools and guidance to carry out the assessment as effectively as possible. In the future, our QA department will perform this task independently.
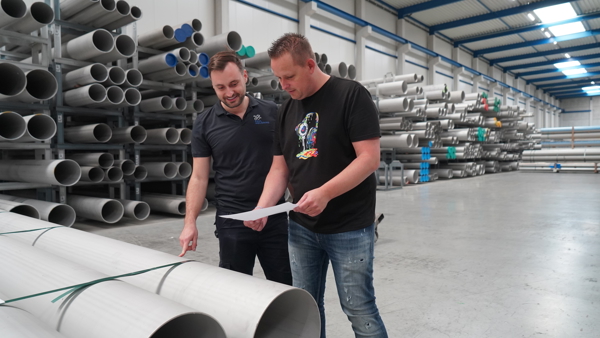
External
Audits
External audits are carried out by Lloyds. In principle, the same aspects are tested in external audits as in an internal inspection, but the outcome of the external inspection is decisive. If the inspection is approved, the ISO certificate is renewed for a year.
For resolving complaints, we use the programme Pro-aQt. With this, all data can be stored in the programme. In addition, it is tracked how many complaints come in each month, what the complaint is about, and where it went wrong. Through this feedback, we can prevent errors in the future.
Material measurements
Measuring equipment
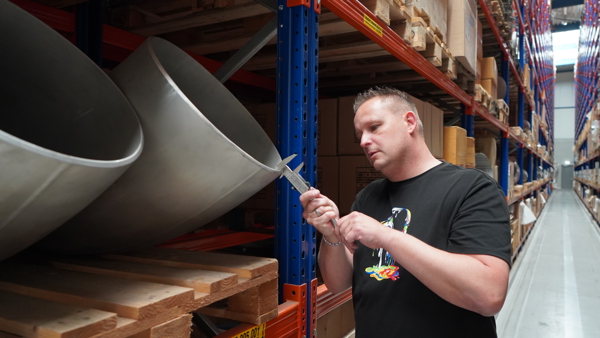
These measurements
to be done with
- Digital calipers for measuring outer diameter, width, and thickness
- An ultrasonic thickness gauge for measuring the wall thickness of pipes
- A Vulcan Handheld analyser for quality control of materials (304, 316, 310, 321, etc.)
In addition to the measuring instruments used by warehouse employees during daily measurements, we also have a Hitachi PMI master pro and an optical emission spectrometer at our disposal.
For us, the saying goes: "measuring is knowing" and "trust is good, but control is better."”
QA manager
Sten Stolzenbach
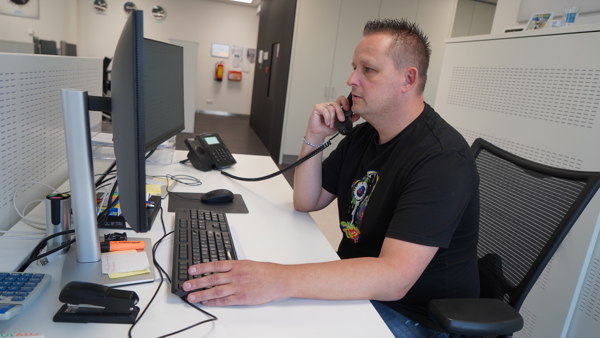
Sten Stolzenbach
quality manager
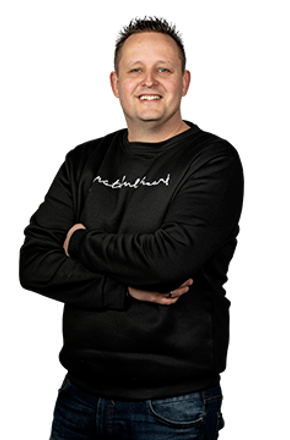